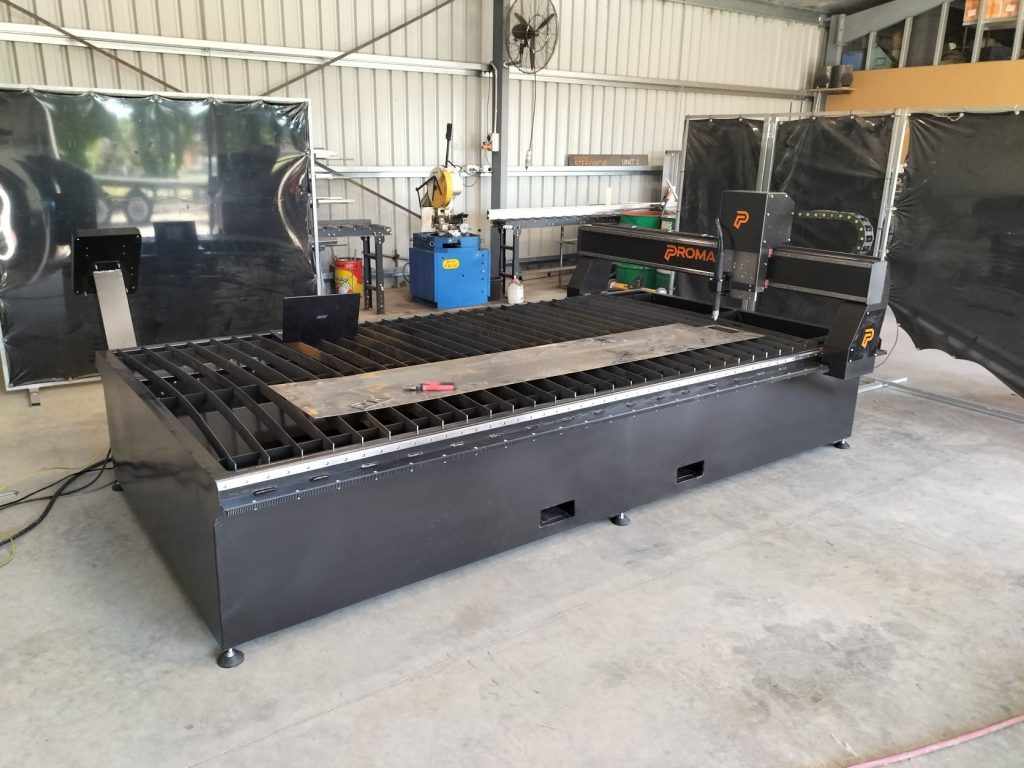
In the world of metal fabrication, precision and efficiency are paramount. A CNC table for plasma cutter combines cutting-edge technology with user-friendly features to revolutionize the way metals are cut. Whether you are a hobbyist or a professional fabricator, investing in a plasma cutting CNC table can significantly enhance your workflow. This guide delves into what a CNC table for plasma cutting is, its benefits, and how to choose the right one for your needs.
What Is a CNC Table for Plasma Cutter?
A CNC (Computer Numerical Control) table for plasma cutter is a specialized piece of equipment designed to automate the plasma cutting process. The table holds the material in place while a CNC-controlled plasma torch cuts through metals with high precision. This system leverages computer programming to create intricate shapes, patterns, and cuts with minimal manual intervention.
How Does a CNC Plasma Cutting Table Work?
The operation of a CNC plasma cutting table can be summarized in a few steps:
Design Creation: A design or pattern is created using CAD (Computer-Aided Design) software.
Programming: The design is converted into machine-readable G-code, which guides the plasma cutter’s movements.
Material Setup: The metal to be cut is placed securely on the CNC table.
Cutting: The CNC system controls the plasma torch, cutting through the metal with a high-temperature plasma arc.
Finished Product: The result is a clean, precise cut that requires minimal post-processing.
Benefits of Using a CNC Table for Plasma Cutting
1. Enhanced Precision
Manual plasma cutting can be inconsistent, especially for complex designs. A CNC table ensures every cut is accurate, meeting tight tolerances.
2. Increased Efficiency
Automation reduces cutting time significantly. The CNC system can handle repetitive tasks without fatigue, allowing you to focus on other aspects of your project.
3. Versatility
CNC plasma tables are compatible with various metals, including steel, aluminum, brass, and copper. This makes them ideal for a wide range of applications, from industrial fabrication to artistic projects.
4. Cost Savings
Although the initial investment may be substantial, the long-term savings from reduced material wastage and improved productivity make CNC plasma tables a cost-effective choice.
5. User-Friendly Technology
Modern CNC plasma cutting tables come with intuitive software and interfaces, making them accessible even for beginners.
Key Features to Look for in a CNC Plasma Cutting Table
When choosing a CNC plasma cutting table, consider the following features:
1. Table Size
The size of the table determines the maximum material dimensions you can cut. Choose a size based on your typical project requirements.
2. Cutting Speed
Look for a model with adjustable cutting speeds to handle various materials and thicknesses efficiently.
3. Durability
The table’s build quality is crucial. Opt for a model with a sturdy steel frame to withstand heavy use and ensure longevity.
4. Software Compatibility
Ensure the CNC system supports common CAD and CAM software to simplify design creation and programming.
5. Height Control
Automatic torch height control maintains a consistent distance between the plasma torch and the material, ensuring clean cuts and prolonging torch life.
6. Dust and Fume Management
Plasma cutting generates heat and fumes. Look for tables with built-in ventilation or water beds to minimize mess and ensure a safe working environment.
Applications of CNC Plasma Cutting Tables
CNC plasma cutting tables are used in various industries and applications, including:
Automotive Manufacturing: Cutting parts for vehicles.
Construction: Fabricating structural components.
Art and Design: Creating intricate metal sculptures and signs.
Aerospace: Producing high-precision aircraft parts.
Small Businesses: Enabling custom fabrication for clients.
Tips for Maintaining Your CNC Plasma Cutting Table
Proper maintenance ensures your CNC plasma table performs optimally for years. Here are some tips:
Regular Cleaning: Remove metal debris and dust from the table and torch after each use.
Inspect Consumables: Check and replace nozzles, electrodes, and other consumables as needed.
Calibrate the Machine: Periodically calibrate the CNC system to maintain cutting accuracy.
Lubricate Moving Parts: Keep the rails and gears lubricated to prevent wear and tear.
Monitor Software Updates: Stay updated with the latest software versions for improved functionality and security.
Top CNC Plasma Cutting Table Brands
When shopping for a CNC plasma cutting table, consider reputable brands known for quality and reliability. Some popular options include:
Hypertherm: Renowned for its precision and advanced technology.
Lincoln Electric: Offers durable and versatile models.
Torchmate: Known for user-friendly systems.
Baileigh Industrial: Provides robust tables suitable for heavy-duty use.
CrossFire: A budget-friendly option for hobbyists and small businesses.
Final Thoughts
A CNC table for plasma cutter is an invaluable tool for anyone working with metal. Its ability to deliver precision, efficiency, and versatility makes it a game-changer in the fabrication industry. By choosing the right table and maintaining it properly, you can streamline your workflow and achieve professional results every time. Whether you’re a seasoned professional or a DIY enthusiast, investing in a CNC plasma cutting table is a step toward improved productivity and creativity. Explore your options, compare features, and find a model that fits your needs and budget.
Write a comment ...